- Home
- Knowledge Base
- How to Choose the Aluminum Alloy Manufacturing Method?
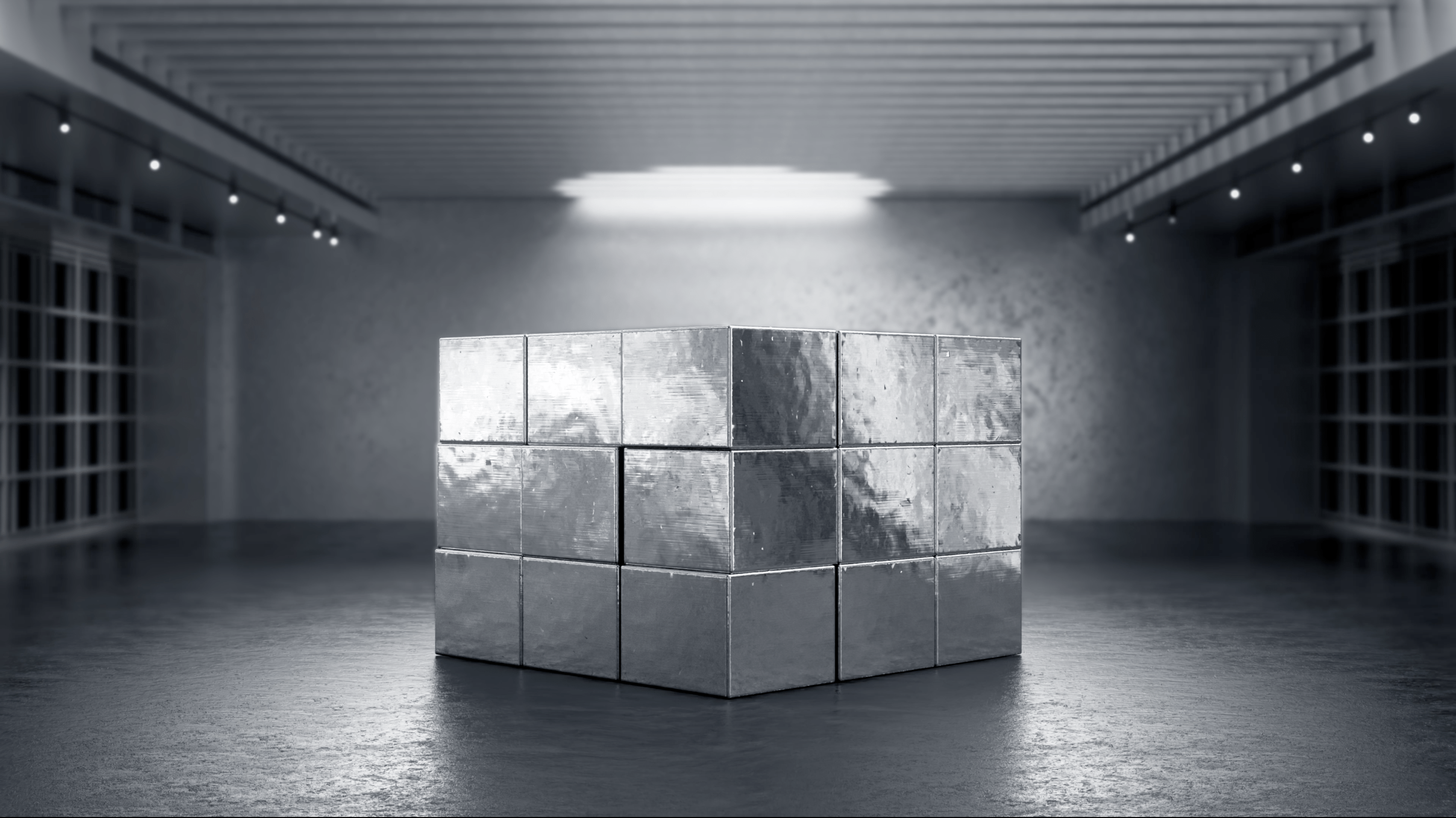
Gravity Casting is a casting method that uses the force of gravity to pour molten aluminum into molds. Despite its slower injection speed, it offers high stability. Gravity casting is suitable for manufacturing large and complex products, such as automobile engine cylinders and mechanical components. It can provide high-quality products while reducing the presence of air voids and internal stress. Additionally, the process requirements for gravity casting are relatively low, as it does not require additional high-pressure equipment, and the mold's lifespan requirements are lower, resulting in relatively lower costs.
Die Casting is a casting method that uses high-pressure injection to rapidly fill molds with molten aluminum alloy. Die casting is characterized by fast injection and filling and is suitable for high-volume and rapid production of products like automotive parts and household appliances. Die casting typically offers high production efficiency and short cycle times. However, die casting has higher process requirements, necessitating high-pressure equipment and precision mold designs, which can result in higher equipment and maintenance costs.
The features of Different Casting:
For Gravity Casting Production
1. If there are strength requirements, and the parts will be used in mechanical products or mechanisms, it is recommended to use gravity casting.
2. Gravity casting naturally solidifies as it cools, resulting in strong structures. Although it has a slower production speed and slightly higher unit costs, it can meet various requirements, and each batch typically requires orders of 200 to 1,000 pieces per batch.
For Die Casting Production
1. If there are no strength requirements, and the parts will be used for aesthetic purposes or lightweight components, die casting is the preferred method.
2. Die casting offers a faster production speed and lower unit costs. Each batch typically requires orders of 1,000 to 5,000 pieces per batch (depending on the size and weight of the product) and has a minimum weight requirement.
For Aluminum Extrusion Production
1. Alternatively, parts can be formed using the extrusion method, and they can meet strength requirements after heat treatment.
2. The main difference is that after extrusion, post-processing often involves multi-axis CNC machining for final shaping. Extrusion is fast and cost-effective, but the minimum order quantity for each extrusion is typically 200 kg to 500 kg per run. If the minimum order quantity cannot be met, additional tooling costs may apply.